KTG Memphis
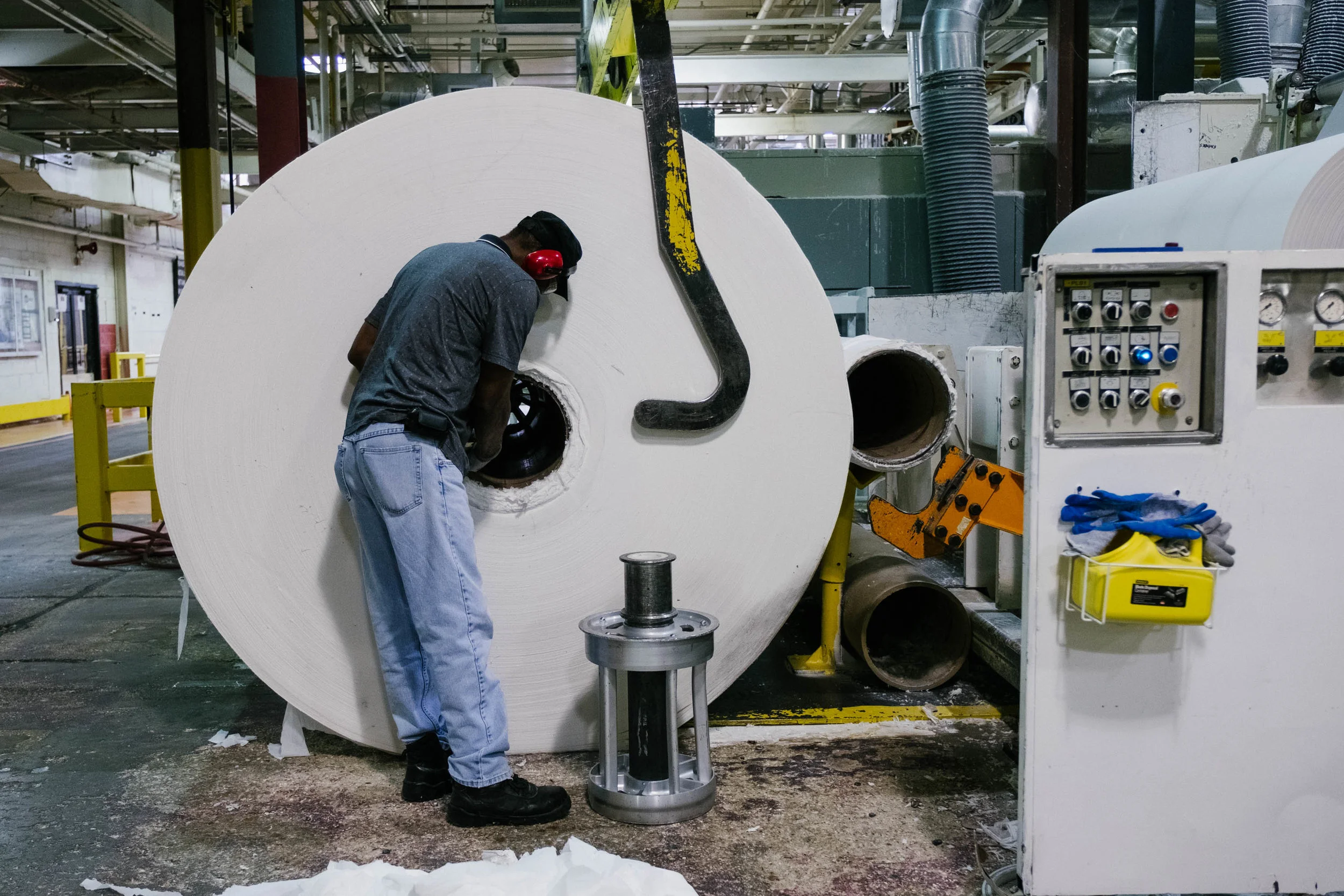





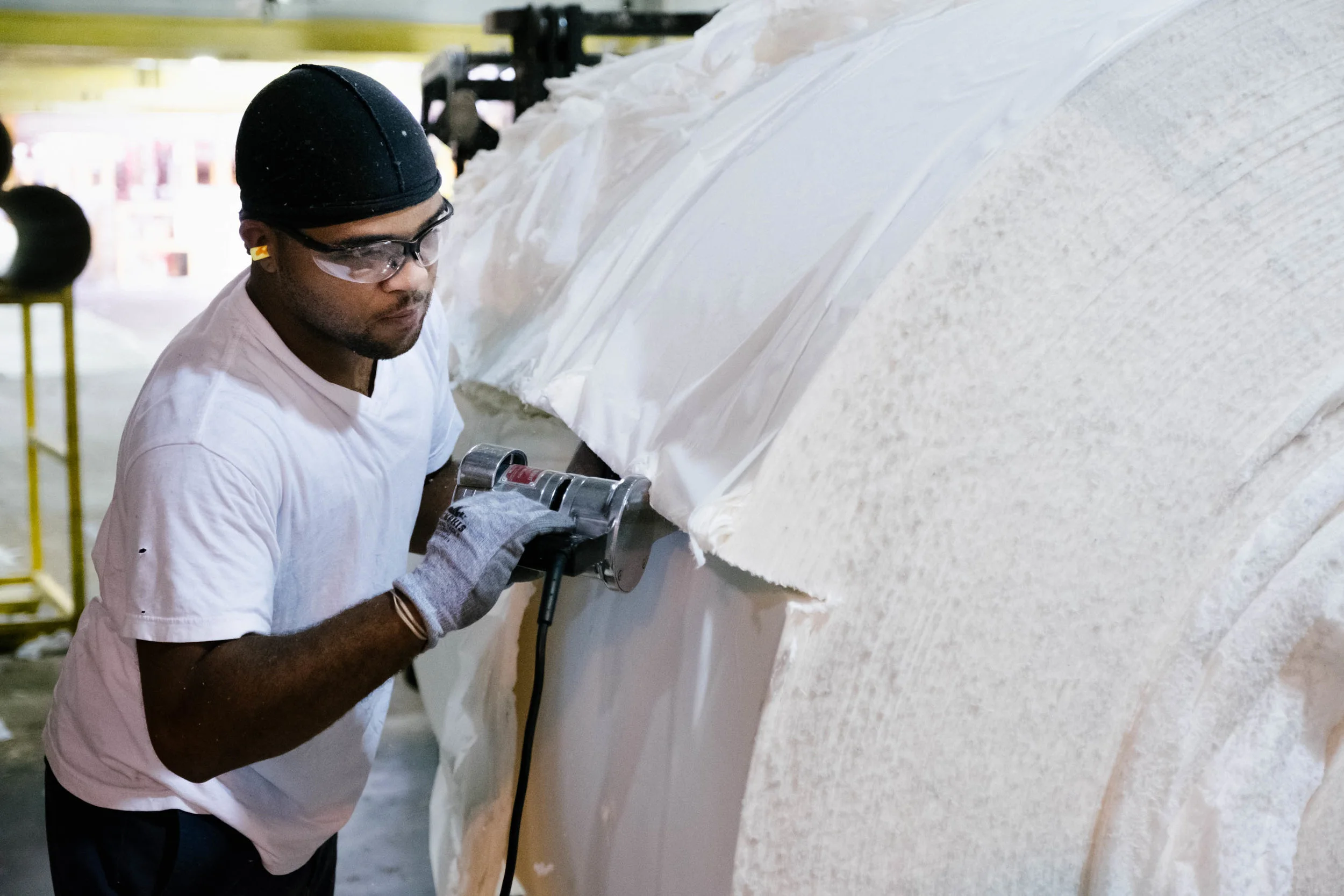












In northern Uptown, the KTG paper mill is at the heart of industry in the neighborhood.
Located in the northern part of Uptown, KTG USA is not a spot one immediately considers when thinking about anchors of the north Downtown neighborhood. Situated between a variety of businesses, from the stables for Downtown’s carriage horses to concrete manufacturers and metal recyclers, the KTG USA paper mill is squarely positioned in a purely industrial part of town.
This area, largely surrounded by undeveloped land, feels as though it is separate from the postcard sights Memphis residents are accustomed to visiting like St. Jude Children's Research Hospital and the Bass Pro Shop at the Pyramid.
This industrial pocket is a significant element of this neighborhood, and KTG USA, located at 400 Mahannah Avenue, is a substantial piece of this jigsaw of industry in this part of Uptown.
KTG USA was formed after their Canadian parent company acquired the Uptown facility, located at 400 Mahannah, in 2002. Presently, it is the only KTG manufacturing facility in the United States. The plant processes and packages toilet paper for brands such as White Cloud for distribution across North America.
Darrel Brown, 28, has worked in the plant for eight years. “This is my first job,” he said, and he has no intention of leaving anytime soon. “I want to make a career out of this.” Part of Brown’s enthusiasm stems from the nature of task — in his words, “getting paid to cut stuff up.”
Brown processes product that doesn’t meet quality control standards so that it can be recycled. KTG wastes as little raw material as possible and these quality standards are exacting as the product is used in intimate proximity to the human body.
Brown's step in the production process is an early one. Bales of pulp and recycled material are mixed into large vats, called pulpers, and combined with water until a certain consistency is reached. The pulp is then put through a series of rollers which press out all of the water and flatten it into long, thin lengths of paper. This is then cut up and “bleached,” a process that is a trade secret and avoids the use of any toxic chemicals. The wet pulp is then dried into thin paper and spooled into what are called parent rolls.
Each parent roll holds about forty-six miles worth of paper. These parent rolls are eventually fed onto smaller, long cardboard tubes to create logs. These are essentially wide rolls of toilet paper as we know it and are eventually cut into individual rolls that can then be inspected and packaged for sale. The final product is loaded onto trucks and makes its way across the United States and to Canada.
The work is often difficult and requires concentration and caution from the employees who operate these machines. It isn’t difficult to become seriously injured during any stage of the manufacturing process. KTG takes employee safety seriously, and since 2009, has been able to significantly reduce the number of on-site injuries and safety violations. Fred Ceruti, the plant’s general manager, is fond of saying with a smile, “at the end of the day, we’re just making toilet paper.”